At CES 2024 in Las Vegas from January 9–12, Hyundai Motor Company exhibited future technologies from Hyundai Motor Group. Under the theme ‘Ease every way,’ the company redefined its role in creating a more comfortable everyday life. The focus extended beyond mobility, aiming to innovate a human-centered life by completing a hydrogen energy ecosystem and shifting toward software-driven approaches.
Hyundai Motor’s exhibition at CES, located in the West Hall of the Las Vegas Convention Center (LVCC), was three times larger than its display at CES 2022, covering an area of around 21,600 sq. ft. The exhibition featured displays showcasing hydrogen, ‘software-defined vehicle’ (SDV), and artificial intelligence (AI)-related technologies. The goal was to realize a safe and free future for society.
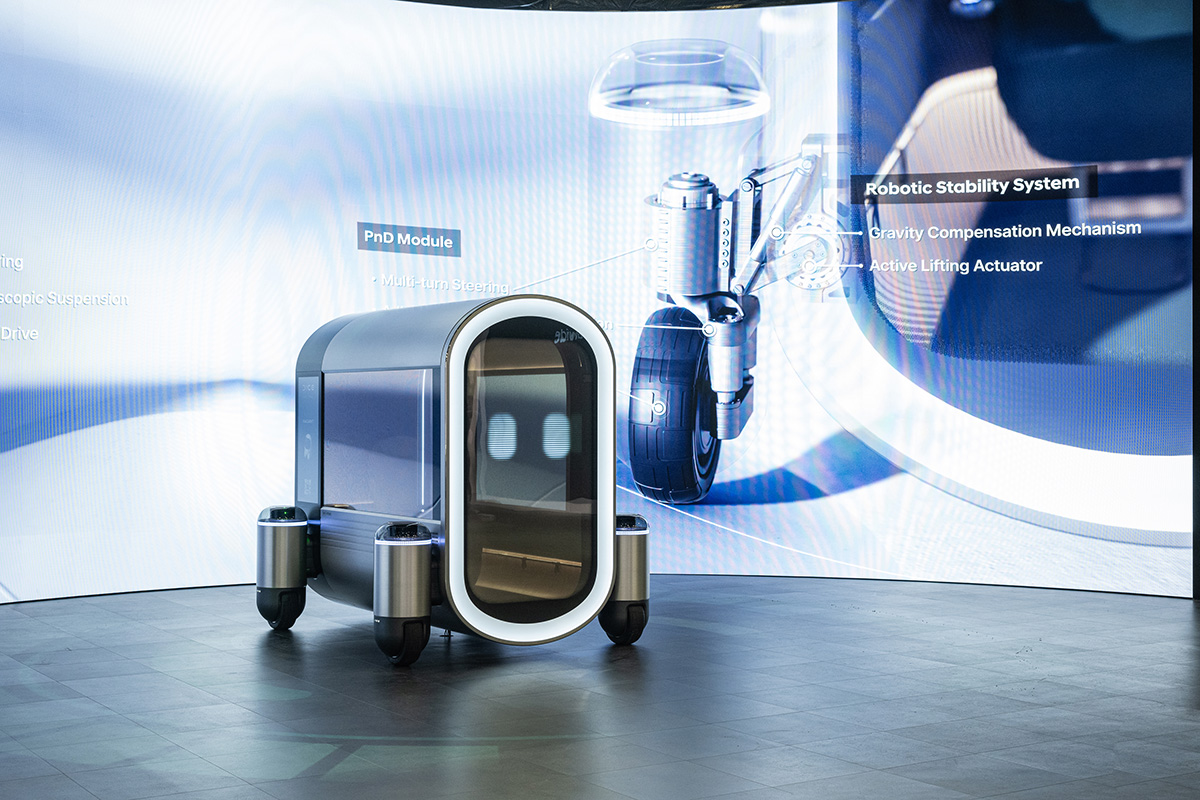
Through this exhibition, Hyundai Motor aimed to provide customers with an experiential journey into the human-centered future vision. Key demonstrative technologies in hydrogen and software, along with future mobility concepts, were introduced to showcase the company’s commitment to shaping a safer and more liberated future.
In 2021, Hyundai Motor committed to achieving carbon neutrality by 2045 and made ongoing efforts to reduce carbon throughout its value chain. At CES 2024, Hyundai Motor expanded its existing fuel cell brand, HTWO, into the Group’s hydrogen value chain business brand, introducing the ‘HTWO Grid’ solution to accelerate the transition to a hydrogen society.
HTWO utilized the capabilities of each affiliate within the Group, offering an optimized package that integrated unit solutions (‘Grid’) to meet diverse environmental characteristics and customer needs across hydrogen production, storage, transportation, and utilization. Hyundai Motor showcased its future direction at CES through a media table examining technologies applied at each value chain stage, emphasizing the expedited transition to a hydrogen society.
At the production stage table, visitors explored resource-circulating hydrogen production technology, including Plastic-to-Hydrogen (P2H), Waste-to-Hydrogen (W2H), and a green hydrogen process. P2H involved melting non-recyclable waste plastics, transformed into clean hydrogen energy through a combination of liquefaction technology from Hyundai Engineering and gasification technology from Shell. W2H converted biogas from organic waste into hydrogen, with Hyundai Engineering & Construction (E&C) and Hyundai Rotem collaborating to enhance technological development. The W2H Process Diorama illustrated the process from biogas collection to hydrogen production, carbon capture, and hydrogen-refueling stations.
Visitors learned about green hydrogen produced by electrolyzing water, operating electrolysis plants on renewable energy sources like wind, solar, and hydropower. As a carbon-free energy source, green hydrogen gained attention as an ultimate clean energy future. Hyundai E&C and Hyundai Engineering participated in constructing electrolysis-based green hydrogen production facilities in Buan and Boryeong, South Korea.
Hydrogen storage and transportation were detailed, with Hyundai Glovis establishing a hydrogen logistics business process and utilizing ammonia carriers for transportation. Hyundai Glovis strengthened capabilities in hydrogen transportation, managing a hydrogen supply flow through production, shipping, transportation, and consumption stages. Hyundai Glovis successfully procured orders for ammonia transport carriers, advancing maritime transportation capabilities in hydrogen energy.
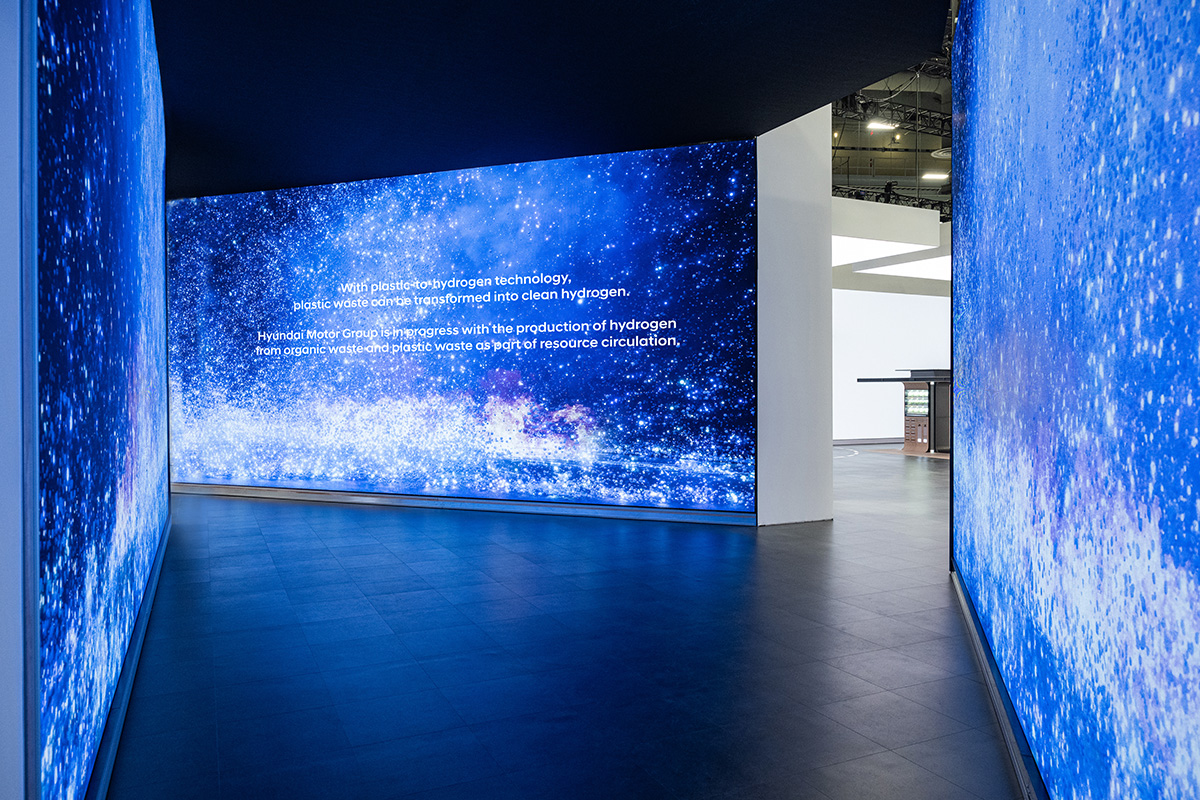
Hyundai Glovis handled hydrogen transportation from the Dangjin hydrogen shipping center to hydrogen fueling stations, coordinating fueling schedules, dispatch plans for tube trailers, and establishing a systematic hydrogen logistics business. The company’s efforts reflected a dedicated commitment to realizing the hydrogen vision at the Group level, showcased through a video at the CES booth, highlighting hydrogen demonstration projects and core technologies conducted by the group during the past event.
Hyundai Motor’s XCIENT Fuel Cell made history as the world’s first mass-produced fuel cell Class 8 heavy-duty truck. It gained recognition for its eco-friendliness and technological prowess in major global markets, notably in Switzerland and Germany. The company successfully launched tractor models specifically tailored for the North American market.
During the past event, Hyundai Motor strengthened collaborations with partners, including global e-commerce players, focusing on green logistics transformation. The commitment to providing optimized hydrogen mobility solutions was evident, building on the foundation of its hydrogen fuel cell trucks.
On display was the mobile fuel cell generator, capable of supplying electricity solely through the fuel cell stack without the need for additional auxiliary power storage devices. This generator proved valuable in various fields and could provide power during emergencies, such as power outages or challenging environments with limited access to alternative power sources.
The mobile fuel cell generator played an active role in Electric Touring Car Racing (ETCR) competitions. Hyundai Motor established a charging infrastructure using its hydrogen fuel cell system to ensure seamless operation for all participating companies in the competition. Racing cars in the ETCR series recharged their batteries using electricity generated by the fuel cell generator produced by the Group.
Adjacent to the media table, a sectional model illustrated the operating principle of a portable hydrogen fuel cell generator, allowing visitors to examine its structure in detail for easy understanding.
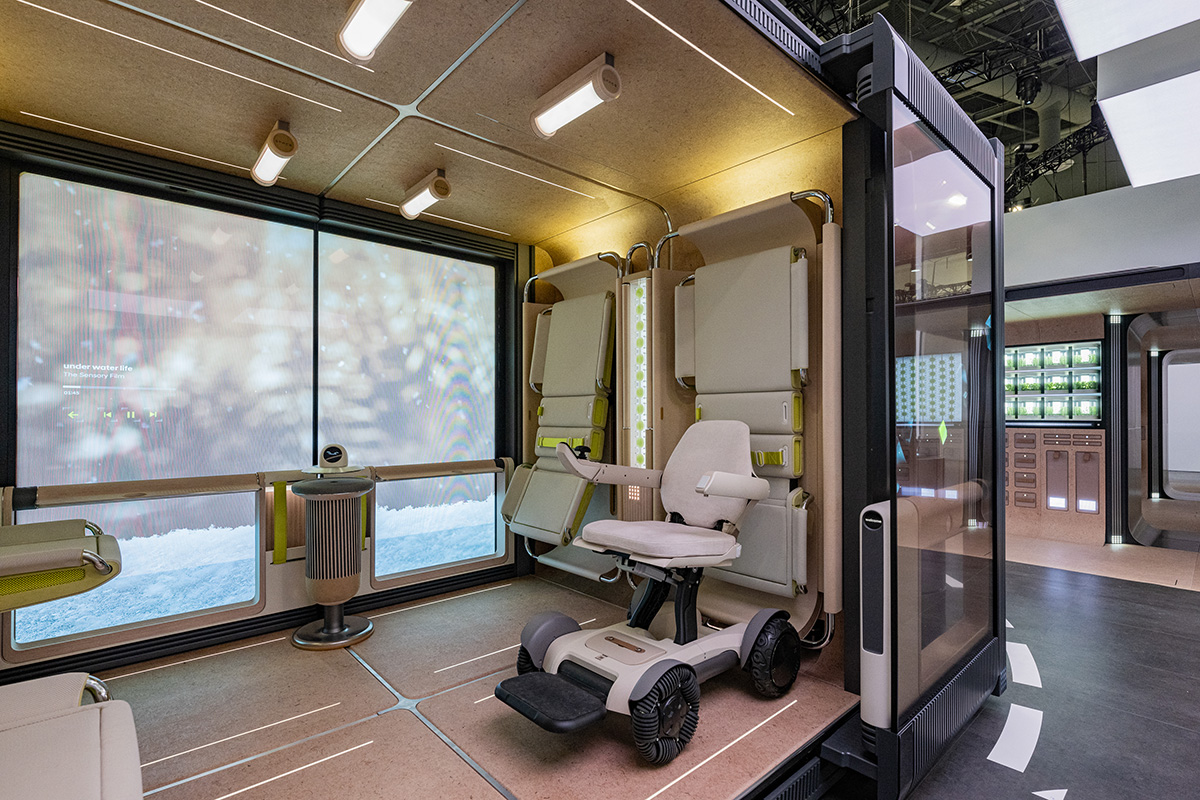
The hydrogen fuel cell tram, designed for environmentally friendly public transportation, contributed to the purification and production of clean air. Equipped with four hydrogen fuel cells with a capacity of 95 kW, the tram could travel up to 150 km. It purified approximately 800 μg of fine dust and produced 107.6 kg of clean air per hour of operation. The wireless design eliminated the need for tram overhead lines, enhancing the city’s aesthetics and reducing infrastructure costs. Hyundai Rotem planned to expand its lineup, including hydrogen high-speed trains, electric multiple units, and locomotives.
Booth visitors learned about Hyundai Steel’s initiative to establish a green steel production system, aiming to cut carbon emissions in the steel production process. The company aimed to reduce both direct and indirect carbon emissions by 12 percent by 2030 and achieve net-zero emissions by 2050. By introducing eco-friendly processes, such as replacing blast furnaces with electric arc furnaces and utilizing hydrogen and renewable energy instead of coal energy, carbon emissions in the steel production process were significantly reduced.
Hyundai Motor presented exhibits and videos introducing core technologies under development by the Group’s global software center, 42dot. The focus was on ‘software-defined vehicle’ (SDV) technologies, emphasizing the role of software (SW) and artificial intelligence (AI) in becoming a smart mobility solutions provider.
Hyundai Motor aimed to redefine various aspects, extending from vehicles to surrounding environments, using SW and AI. The CES exhibit highlighted the Group’s existing practical software-defined mobility services and technologies supporting the expansion from SDV to SDx (‘Software-defined Everything’).
The SDV Electrical/Electronic (E/E) Architecture took center stage, representing the core hardware structure of SDV. It showcased the operational framework and functional structure where the vehicle’s cameras, radars, and sensors gathered driving environment data, enabling autonomous driving through the integrated controller, a High-Performance Vehicle Computer (HPVC) embedded within the vehicle. The exhibit illustrated the simplification of the vehicle’s hardware structure during the transition to SDV, providing a more intuitive view.
In front of the exhibit, driving scenes in Pangyo, South Korea were displayed, showcasing actual road scenarios like left and right turns. The staged scenarios illustrated the data flow where the HPVC and zone controllers for autonomous driving were activated based on the road environment. LED lights visualized this flow. Additionally, the exhibit allowed observation of the operation of a ‘fault-tolerant’ function within SDV safety features, demonstrating that even if one controller malfunctioned, another controller would take over to ensure safe driving.
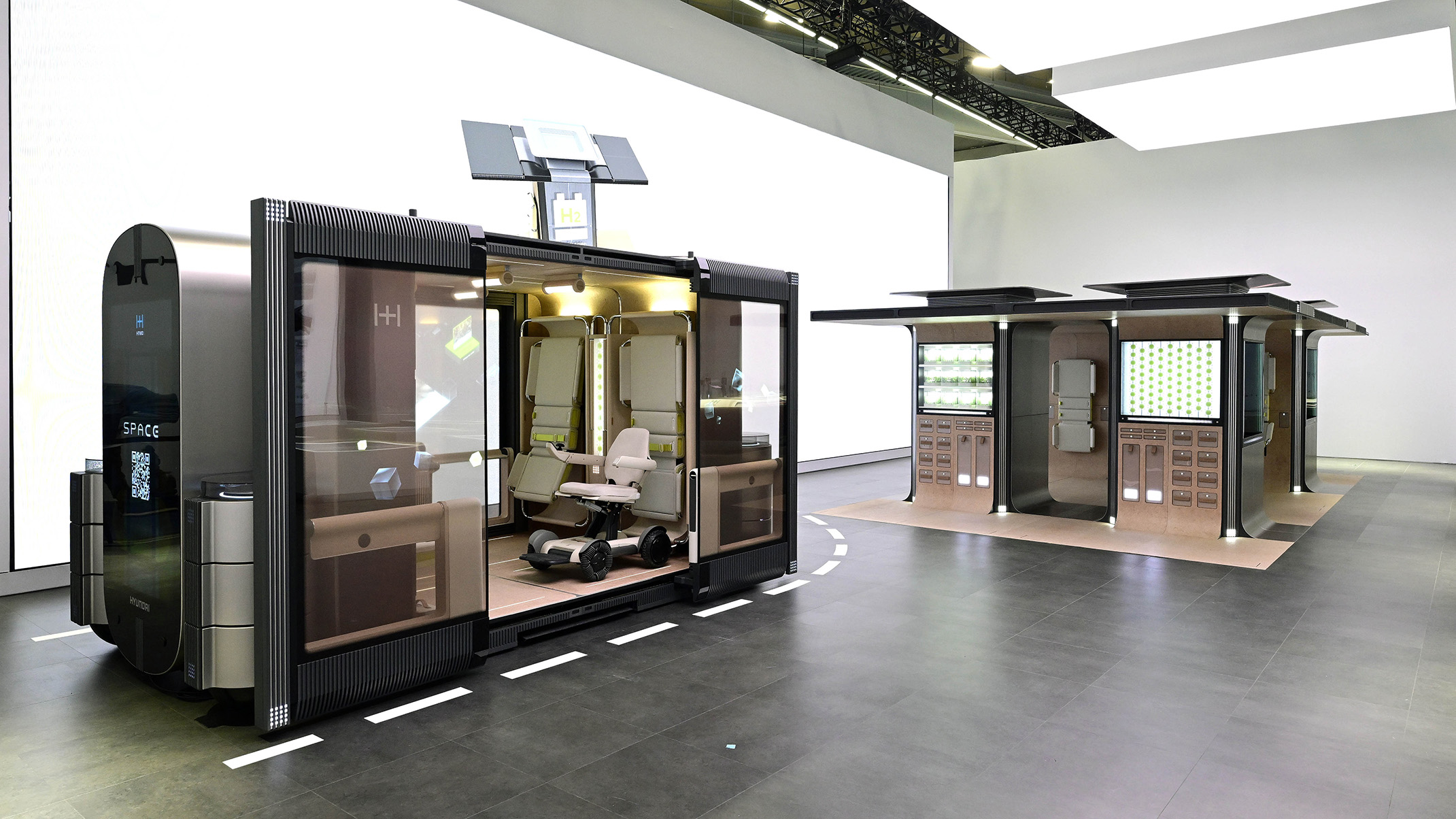
The HPVC, exhibited alongside the SDV architecture, served as the integrated hardware consolidating core SDV technologies. It controlled all other controllers within the SDV, functioning as the brain of the SDV and enabling the application of software technologies in the vehicle. The HPVC played a significant role in enhancing the vehicle’s performance, safety, and convenience.
Two HPVC models developed by 42dot were available at one of the six media tables in the central software section within the booth. These models differed in their cooling methods: one used air cooling, dissipating heat through the air, while the other utilized liquid cooling with water.
42dot had not only developed HPVC and controllers but also worked on an SDV operating system, SDV OS, ensuring the stable and efficient operation of in-vehicle applications. Positioned to the right and above the HPVC exhibits, additional five media tables allowed visitors to watch videos introducing the five core SDV technologies developed by 42dot and a film showcasing various Group-wide practical software-defined mobility services in motion that were operational.
The videos introduced the following five core technologies:
1. HPVC and SDV OS: A modern data center-like network architecture and a fault-tolerant system for SDVs.
2. Data-Driven Learning Systems: Continuous integration and deployment of autonomous driving from R&D to commercial robo-taxi service through MLOps and DataOps.
3. Safety-Designed Vehicle: Technology focused on cybersecurity and safe driving control.
4. LLM for Advanced Mobility: Conversational AI assistant enhancing human-like interaction between SDVs and drivers/passengers.
5. Self-Managed Smart City: SDV technologies extending beyond vehicles into the city.
Additionally, Hyundai Motor presented a video on software-defined mobility services in motion, equipped with advanced technologies operated by various companies within the Group. The video featured the on-demand shuttle ‘Shucle,’ the autonomous mobility platform ‘TAP!,’ and Motional’s IONIQ 5-based autonomous taxi service ‘Robotaxi.’
The Group unveiled a hydrogen-based mobility service concept, connecting everyone’s life and providing a convenient and free movement experience in line with the vision of ‘Ease every way,’ as presented at CES 2024. In the exhibition, visitors explored the Group’s future mobility solutions, spanning from personal mobility to public mobility and logistics, realizing a human-centered vision that extended from individuals to cities.
DICE (Digital Curated Experience), infused with AI, served as a personal mobility platform providing curated services through customized software technology. A display surrounded on three sides allowed for a more immersive mobile experience. The ‘Ring Pad’ controller, a kinetic interface evolved from existing vehicles, facilitated communication with AI and adjustment of the DICE environment, incorporating a bio-sensing camera for optimization and an airbag for safety.
When used for travel, DICE offered curated journey suggestions based on personal device integration, considering the user’s schedule and destination. Additionally, it could reroute in response to sudden schedule changes and activate ‘Therapy Mode,’ monitoring the user’s condition through continuous bio-sensing. Hyundai aimed to showcase the evolution into a platform with infinite possibilities, transcending traditional driver-passenger roles through spatial computing-based interfaces of DICE.
While DICE focused on personalized digital experiences during transportation, SPACE (Spatial Curated Experience) aimed to provide customized spatial experiences by incorporating individual lifestyles into the mobility space, embracing users across a wide spectrum of needs, along with free mobility.
SPACE Mobility addressed varied passenger needs with optimized space and adaptive seats, supporting wheelchair users, micro-mobility users, and pets through comfortable boarding height control. Booth visitors could enjoy customized content through a large transparent display on doors, while the AI service agent interacted with users, providing necessary information throughout the journey.
SPACE extended to an open area called the ‘Pavilion,’ constructed from reused obsolete mobility modules. It architecturally reinterpreted the life cycle of mobility, imparting various functions and usability to each module. The Pavilion interacted with the software environment through a hologram interface, offering portable battery slots and various charging modules for sharing energy through a hydrogen fuel cell system. It functioned as a hub connecting people, city, robot, and mobility, incorporating an air-cleaning algae module and a smart farm that utilized water from the byproduct of a hydrogen fuel cell, along with a rest area featuring mobility seats.
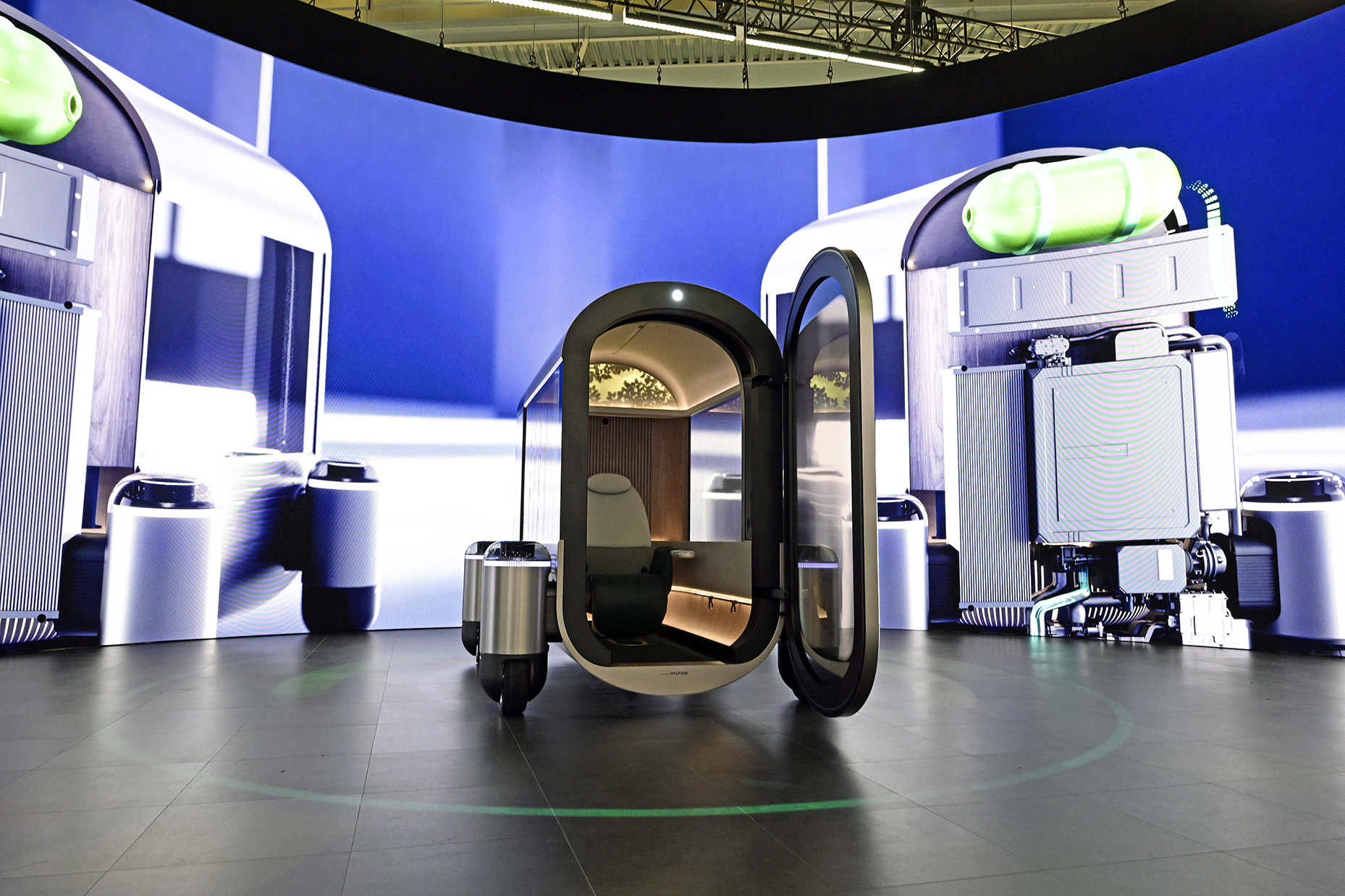
Also on display was CITY POD, an unmanned large-scale mobility system that surpassed the limits of existing logistics systems based on software. It presented an ‘automatic logistics sorting system’ that moved organically and actively at all stages.
CITY POD, utilizing hydrogen energy technology, adopted a modular system combining Plug & Drive and PnD POD, showcasing an efficient and systematic middle mile and last mile logistics vision. Each POD was automatically combined or separated as needed, enabling logistics to be delivered directly to customers not only on the road but also inside buildings.
In addition, Hyundai Motor also exhibited ‘Stretch,’ a logistics loading and unloading robot developed by Boston Dynamics. ‘Stretch’ was an autonomous robot designed for more efficient and safer logistics operations, primarily assisting in emptying loaded trailers and shipping containers in warehouses.
Stretch used AI to make real-time decisions on all boxes and sorted logistics according to self-established rules, eliminating the need for entering additional information in advance. Its main feature was the ability to carry boxes weighing up to 50 pounds (approximately 22.7 kg) and even pick up multiple boxes at once. At the booth, Stretch continuously demonstrated picking up and putting down a box on the floor.
Discover more from SNAP TASTE
Subscribe to get the latest posts sent to your email.